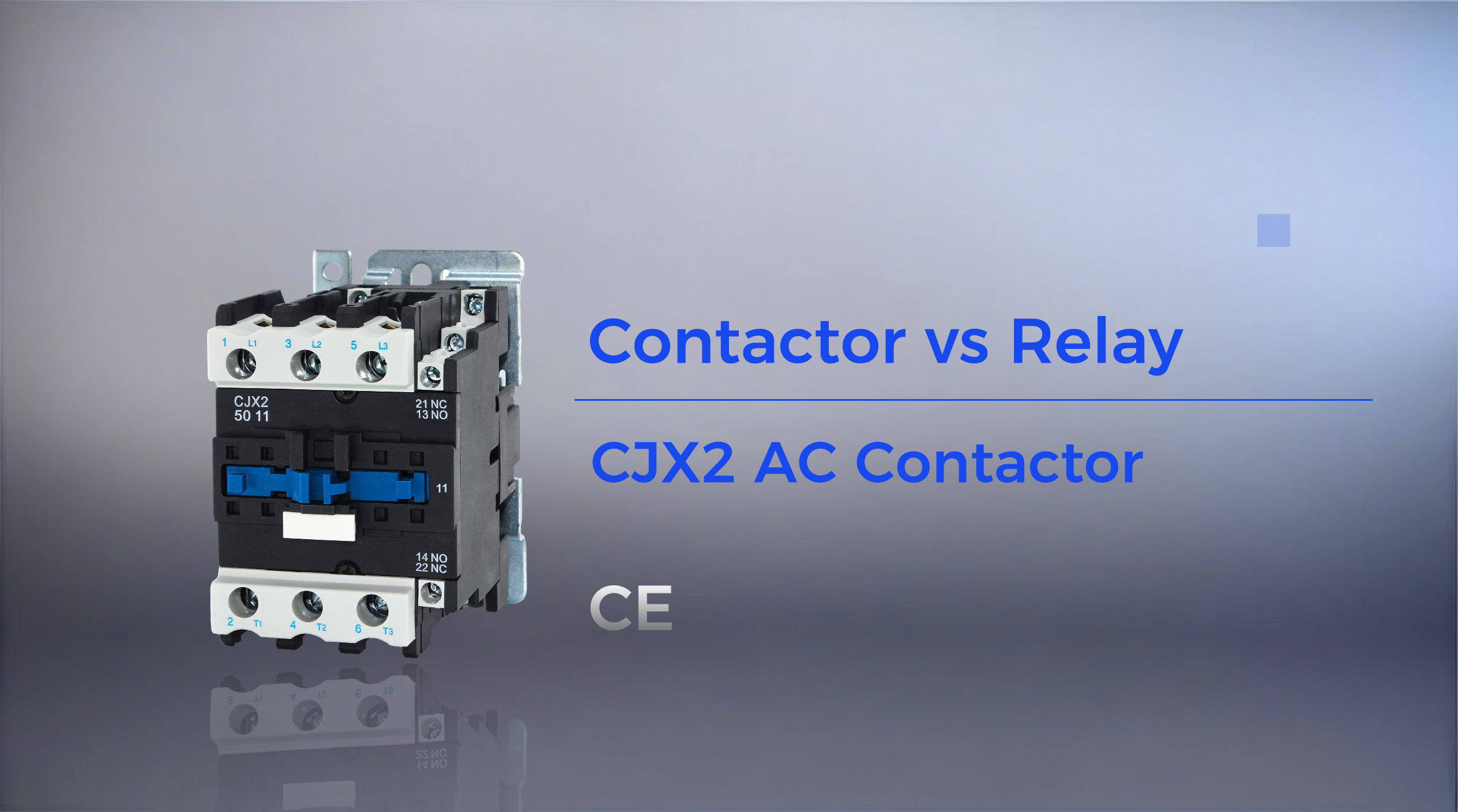
Electromechanical switches like contactors and relays silently power industrial systems—but choosing wrong risks costly failures. Contactor vs relay isn’t just semantics: one handles heavy loads (10A–1000A) for motors, while the other manages low-power signals in PLCs. Let’s cut through the technical fog. Why care? Engineers optimizing conveyor belts or smart factories need precision—mismatching these can fry circuits or cripple automation. Think voltage thresholds, arc suppression, and noise tolerance. Your system’s reliability starts here.
What is a Contactor?
A contactor’s power lies in electromagnetic induction—think of it as the heavyweight champion in the contactor vs relay showdown. Built to dominate 10A–1000A loads, its NO (Normally Open) contacts slam shut when energized, channeling raw power to motors or HVAC systems. Three pillars make it industrial-grade: robust coils generating magnetic fields, arc chutes extinguishing dangerous sparks, and precision engineering for 500k+ cycles. Unlike relays handling PLC signals, contactors thrive where brute force matters—like kickstarting a 50hp compressor without melting down. Next time your factory floor hums, thank the contactor silently preventing chaos.
How a Contactor Works: Step-by-Step
Here’s the magic behind the contactor vs relay divide. Energize the coil—a magnetic field erupts, slamming those heavy-duty NO contacts shut to channel 100A+ loads. Unlike relays handling timid PLC signals, contactors brute-force power to industrial motors. Cut the current? The spring snaps contacts open faster than a circuit breaker’s blink, arc chutes smothering sparks that’d fry delicate relays. Picture this: your HVAC compressor roaring to life without meltdowns. That’s a contactor’s silent pact—raw power with zero apologies.
What is a Relay?
Relays are the silent strategists in the contactor vs relay dynamic—think precision over brute force. Their armature physically flips NO/NC contacts to orchestrate low-power signals, isolating PLC systems from high-voltage chaos. Unlike contactors wrestling 100A+ loads, relays thrive in automation logic, where 10A ceilings demand surgical control. Solid-state versions swap moving parts for lightning speed (100k+ cycles!), while electromechanical types endure harsh vibrations. Need proof? Your elevator’s smooth floor stops? That’s a relay team executing micro-switches, unseen but flawless. Choose wisely: brains or brawn?
Relay Types and Specialized Applications
In the contactor vs relay debate, relays shine where finesse beats force. Electromechanical (EMR) units dominate motor control panels, their physical contacts dancing through 10A signals—child’s play for contactors gulping 100A+. Solid-state relays (SSR) thrive in PLC systems, swapping sparks for silent semiconductor precision. Need timed sequences? Timer relays choreograph automation steps, while latching variants “remember” states for energy savings. Thermal overload types? They’re the unsung heroes halting motor meltdowns. Relays whisper control; contactors roar power. Choose based on your battlefield: delicate logic or brute current.
Contactor vs Relay: 7 Critical Differences
Choosing between a contactor and relay isn’t splitting hairs—it’s about matching muscle to mission. Let’s dissect the contactor vs relay showdown across seven battlefields.
1.Load Capacity
Contactors flex industrial-grade strength (10A–1000A, 1000V+), handling motors that’d vaporize relays (<10A, 250V). Picture a contactor powering a factory conveyor versus a relay managing your office’s LED lighting.
2.Safety Features
Arc chutes in contactors smother sparks from 500A breaks—relays? Their basic enclosures suffice for low-risk PLC signals. One guards against infernos; the other prevents hiccups.
3.Contact Configuration
Contactors default to NO (Normally Open) for high-power circuits, slamming shut under load. Relays play both sides—NO/NC contacts adapt to automation logic like traffic lights switching modes.
4.Physical Size
Industrial contactors dominate panels with refrigerator-sized frames. Relays? They tuck into DIN rails like discreet secretaries. Bulk versus brains.
5.Electrical Noise
Contactors roar with EMI interference—shield them near sensitive sensors. Relays whisper, ideal for noise-averse environments like lab equipment control.
6.Lifespan
Contactors endure 500k+ cycles in steel mills; relays falter after 100k rapid PLC switches. Durability vs delicacy.
7.Cost Factors
SSR relays (premium semiconductor tech) can outprice basic three-phase contactors. But skimp on a contactor for heavy loads? Prepare for meltdowns.
Application Scenarios: When to Use Which?
The contactor vs relay choice pivots on power versus precision. Deploy contactors where brute force rules: 400A conveyor belt startups or multi-phase panels feeding industrial giants. Relays? Masters of subtlety—they isolate PLC signals like digital diplomats and dim LEDs without a flicker. Imagine contactors muscle-starting HVAC compressors while relays choreograph a factory’s sensor ballet. Facing 1000V motors? Contactor territory. Need whisper-quiet PLC logic? Relays dominate. Swap their roles, and sparks will expose the mismatch.
Selection Guide
1.Current/voltage requirements?
For contactor vs relay decisions, match amps to ambition: contactors devour 10A–1000A loads (motors), while relays nibble <10A PLC signals.
2.Switching frequency?
EMR relays tap-dance 100k times before retirement; contactors endure 500k+ cycles in steel mills. Choose based on your click rate.
3.Environmental factors?
Contactor arc chutes battle foundry sparks; relays shiver in dust. Climate-controlled panels? Relay turf.
4.Safety certifications?
UL/IEC-certified contactors prevent meltdowns; basic relays handle garage lights. Know your risk level.
5.Budget vs performance?
SSR relays cost more, but skimp on surge-ready contactors? Prepare for fireworks.
Maintenance Tips for Optimal Performance
Keep your contactor vs relay systems humming with surgical precision. For contactors, scrub arc suppressors every six months—carbon buildup here causes 43% of motor failures. Relays demand coil resistance checks: a multimeter reading over 10% spec? Replace it before PLC signals glitch. Hear contactors buzzing like angry bees? That’s arcing begging for attention. Relays failing? Stuck armatures often mean coffee spills or dust invasions. Pro tip: log maintenance dates on your phone. One skipped cleanup could fry a $50k conveyor. Stay sharp—your machines can’t self-heal.
Conclusion & Pro Recommendations
Mastering the contactor vs relay divide isn’t just technical nitpicking—it’s operational survival. Contactors muscle through 1000V motor surges; relays finesse PLC signals with surgical precision. Choose wrong, and downtime becomes your new normal.
WTAI’s UL-certified devices slash failure risks—arc chutes in contactors quench industrial infernos, while relays with gold-plated contacts outlast competitors. Need proof? Their three-phase contactors log 1M+ cycles in cement plants without breaking sweat. Stuck deciding? Grab WTAI’s free consultation—their engineers dissect your load curves and environmental gremlins in 48 hours. Remember: Relays whisper control; contactors roar power. Pick the right warrior for your electrical battlefield.
Post time: Mar-19-2025